The mobilization of employees is an asset and a strength, Veolia has made the development of skills and career paths a priority, as well as the recognition of employees and their performance while respecting their diversity. The company relies on their responsibility and autonomy at all levels and in all countries, and promotes professional equality between men and women.
Discover in this page, the priority objectives of the Group’s human resources performance:
These priority objectives contribute to 5 of the Sustainable Development Goals of the UN: Good health and well-being (SDG 3), Quality education (SDG 4), Gender equality (SDG 5), Decent work and economic growth (SDG 8), Reduced inequalities (SDG 10).
Occupational risk prevention, occupational health and safety are fundamental values within Veolia.
In order to protect the health and safety of each employee in a sustainable manner, Veolia has based its policy on the guiding principles of the International Labour Organization, with the involvement of the trade union and employee representatives. As such, the Group signed the Seoul Declaration at the International Labour Organization headquarters in Geneva on 1 July 2013.
Aware of its responsibility to its employees and partners, the Group is committed to health and safety in all its actions, developing a culture of prevention at all levels.
WHAT ARE THE GROUP’S ACTION PRIORITIES?
- Maintain constant vigilance with regard to risk management and Veolia's compliance with rules and standards in all its activities.;
- Maintain and strengthen Veolia's health and safety prevention culture, as part of a continuous improvement process.
- Identify, analyze and share best practices and proactively develop the Group's standards, in coordination with the members of the Executive Committee.
- Develop research and innovation in prevention, health and safety.
- Maintain and develop the skills of health and safety managers and employees.
- Apply the requirements of the management standards for high-risk activities, which complement local regulations and also apply to Veolia's subcontractors.
- Conduct regular safety visits and audits to help each business unit identify its strengths and areas for improvement.
MULTIFACETED PERFORMANCE INDICATOR (HUMAN RESOURCES DIMENSION) & 2027 TARGET
Health, safety and well-being
Indicator
Lost Time Injury Frequency Rate
2023 reference
2027 target
SOLUTIONS
Strengthen the Group's occupational health and safety culture
Veolia has organized an International Health and Safety Week each year since 2015 in order to deeply anchor health and safety at work in the corporate culture. Identifying lessons learned from crisis management and the adaptations made provide valuable examples to better anticipate risks and promote good practice.
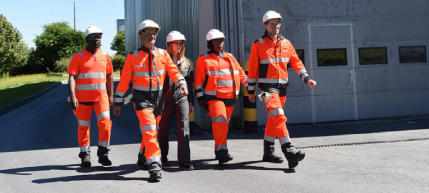
A major risk hunt
As part of the International Health and Safety Week in 2021, an internal photo and video competition was organized at all Veolia sites to identify fall risks based on these photos and videos, which have since been made available on an online platform called "Best Health and Safety Practices" of the Group.
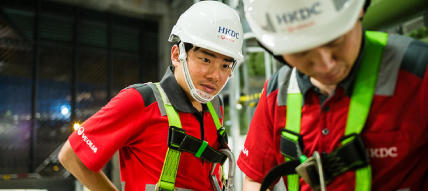
The PaTHS program, a global solution for the management of accidental events
The PaTHS program (Prevention & Training on Health & Safety), currently being deployed, includes a collaborative tool destined for all the occupational health and safety stakeholders within the Group.
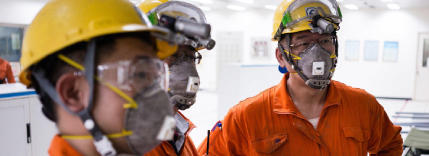
Gender equality in the workplace, support for the United Nations LGBTI standards of conduct for business, and the employment and integration of people with disabilities are key issues for a company's attractiveness, performance and fairness.
A new Diversity & Inclusion action plan was finalized in 2022, with the aim of driving a culture of inclusion that ensures every employee will be treated without discrimination, be recognized in his or her uniqueness and be a full member of the company's community. It is structured around four priority targets: gender diversity; gender identity; disability; and social and ethnic origins.
WHAT ARE THE GROUP’S ACTION PRIORITIES?
Develop gender balance in operations, increase the number of women sitting on the Group’s management bodies and working in management, promote gender diversity in the Group’s representative bodies.
Develop gender diversity in management through:
- recruitment: inclusive recruitment process and young talent policy, creation of a pool of women leaders;
- identification : executive succession plan including at least one woman for each executive, 50% women in staff reviews of high potential by 2023; additional staff reviews for women below the rank of Executive Resourcers;
- development: include 40% of women in the Veolia Excellence program and 30% in the director seminar, develop mentoring by senior managers for high-potential women managers.
Support the United Nations LGBTI standards of conduct for business.
Committing to the following 10 points, following the signature in 2022 of the Business and Disability Charter of the International Labour Organization (ILO): respecting and promoting rights; non-discrimination; equal treatment and equal opportunities; accessibility by gradually making the Group’s premises accessible; maintaining employment so that any person with a disability can keep his or her job; confidentiality of personal information of persons with disabilities; consideration of all types of disability; collaboration through the promotion of employment of people with disabilities; evaluation of integration policies and practices; sharing information about progress on deployed initiatives.
MULTIFACETED PERFORMANCE INDICATOR (HUMAN RESOURCES DIMENSION) & 2027 TARGET
Diversity and inclusion
Indicator
Proportion of women among Group Management Committee
2023 reference
2027 target
SOLUTIONS
Accelerating the Group’s gender balance with the WEDO global network
Veolia’s in-house network dedicated to gender balance, launched in 2016 and sponsored by the members of the executive committee, gathers almost 3,000 employees from 48 countries who want to promote gender balance within the Group.
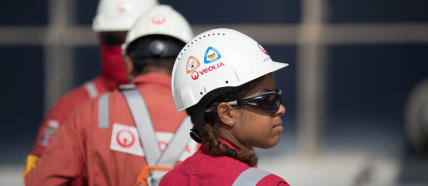
“Women In Leadership”, coaching for women to promote gender equality in business
“Women In Leadership”, initiated by Veolia in North America, has been progressively deployed in other geographical areas: Europe, Africa, Latin America, Asia/Oceania and the Middle East. This eleven-month coaching program aims to create development opportunities for women managers in the organization.
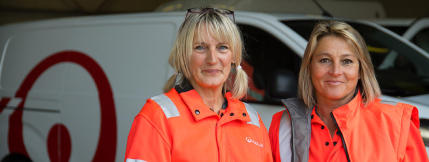
Awareness campaigns aiming to improve consideration for people with disabilities
Several Group entities in various countries have implemented action plans and deployed awareness campaigns, in line with the legal framework specific to each country. In France, for example, an immersive virtual reality experience was proposed in order to remove unconscious bias towards people with invisible disabilities.
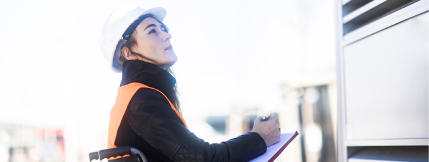
In a changing world, the long-term performance of companies depends on their ability to transform and challenge the status quo. The commitment of their teams is at the heart of this dynamic.
Veolia is both a technology- and labor-intensive company, representing a working community of over 218,000 employees, many of whom are operators and technicians who provide essential services for its customers, the regions in which it operates and society.
It is through sharing a collective project at the heart of its purpose, that of contributing to human progress to achieve a better and more sustainable future for all, that the Group will be able to ensure its ability to transform itself and provide solutions to the environmental and social challenges of today's world.
WHAT ARE THE GROUP’S ACTION PRIORITIES?
- Strengthen and enhance innovation in HR processes and in the dialogue with the Group's employees, enabling the quality and continuity of interactions.
- Support managers in the implementation of new leadership and involvement tools within their teams, as part of a continuous improvement process.
- Ensure that the experience of Veolia employees is always consistent with the Group's purpose and its brand signature "Resourcing the World".
- Correlate the expectations and perceptions of Veolia employees (collected via the Voice of Resourcers commitment survey) with the Group's priority actions to encourage team commitment.
MULTIFACETED PERFORMANCE INDICATOR (HUMAN RESOURCES DIMENSION) & 2027 TARGET
Employee commitment
Indicator
Employee commitment rate
(“Voice of Resourcers” survey)
2023 reference
2027 target
SOLUTIONS
Resourcers for Communities, the commitment of Veolia employees to their regions
“Resourcers for Communities”, initiated by Veolia, is a civic engagement scheme offered to Group employees who wish to get involved with local players (associations, start-ups, small businesses, etc.) by sharing their expertise and know-how.
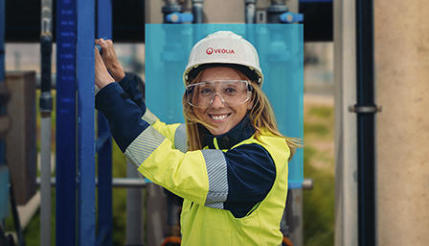
Talent APP: an innovative digital application for skills management
The Talent App was launched in January 2021. It aims to use artificial intelligence to accelerate the development of mobility and cooperation within the Group.
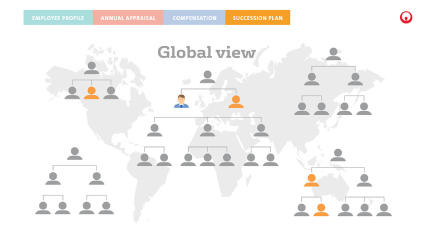
Veolia has made the development of skills and career paths a priority, as well as the recognition of its employees and their performance while respecting their diversity.
In concrete terms, this means anticipating and supporting all employees in the development of their skills in the context of the strategic transformation of the Group, its businesses and its expertise.
The Group has thus adopted an ambitious training and human resources development policy. This policy is based on three objectives: ;
- develop and adapt skills in all professions; ;
- support the performance and commercial development of the Group;
- contribute to the development of the corporate culture.
WHAT ARE THE GROUP’S ACTION PRIORITIES?
- Support the dissemination of the Group's culture, in particular its purpose and multifaceted performance for all.
- Strengthen the Group's culture on the fundamentals of the "non-negotiable" and the challenges of ecological transformation.
- Support and prepare the talents and skills of tomorrow.
- Make the skills of Veolia employees, at all levels of the organization, a lever of competitive advantage and added value for the Group's customers.
- Digitalizing and developing the most innovative methods of skills acquisition.
SOLUTIONS
Virtual reality, an innovative tool for training
In 2020, Poland chose to integrate virtual reality into its training programs. This innovative tool has notably helped to make training modules more attractive to employees, enabled an improvement in skills and their adaptation to the new technologies deployed within the Group.
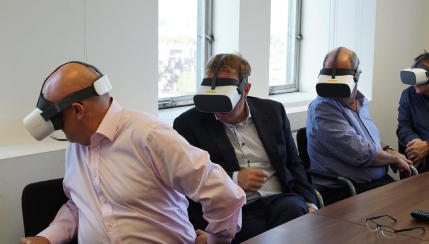
La Fortaleza, a model training center in Latin America for prevention
Since 2016, the La Fortaleza training center, located at the Sede Progreso site in Ecuador, has been providing training to all employees exposed to high risk, whether they are managers or operators. Its facilities allow the trainees to be put in an almost real situation to raise their awareness of the risks and learn to protect themselves by acquiring the right reflexes in the field.
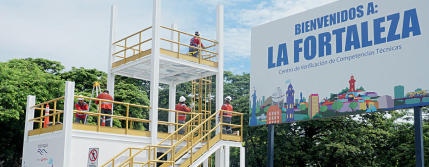
An ambitious project for a School of Ecological Transformation
In 2021, Veolia committed to federating a group of partners (companies, local authorities, public players, employment and training players, trade union and employee representatives) to create a School of Ecological Transformation, with two objectives:
- Promote the highest impact ecological transformation solutions and assessment tools that are most relevant to sustainable development and the planet’s limits;
- Train in the skills and professions of ecological transformation, at all levels of qualification, while targeting in particular people who are unemployed or in retraining.
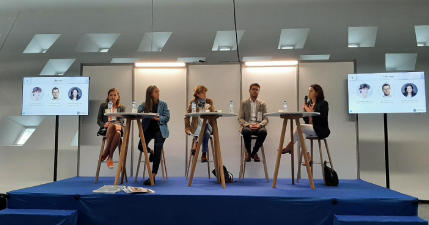