What is biomass?
Biomass is, by definition, organic waste from agriculture, forestry, fisheries and aquaculture as well as biodegradable industrial and municipal waste. Biomass is carbon neutral material that, once converted into a fuel, can be used to generate renewable energy.
Using biomass energy reduces reliance on fossil fuels and helps to secure energy supplies. Biomass is very much a key component of the energy transition.
But biomass is not just for energy. We also need to develop production chains for recovering dry biomass, which is biomass comprising various forms of wood waste, primarily reclaimed wood and wood residues. This then becomes a material that can be reinjected into the wood and papermaking industries.
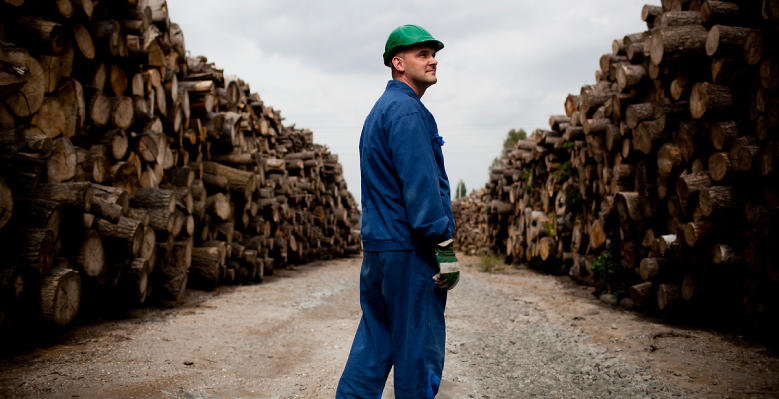
Generating energy from biomass:
In 2019, global capacity for generating electricity from biomass amounted to over 8.5 GW, with China accounting for 5.3 GW, according to the International Energy Agency.
Our solutions for collecting and transforming biomass
With upwards of 500 projects worldwide, we handle our customers’ organic waste, all the way from collection to recovery as energy.
We recover and recycle biomass in two ways:
- as energy, using solutions to produce heat and electricity from biomass on behalf of our industrial and municipal customers;
- as material, using solutions that offer total recycling and recovery of wood waste and offcuts.
We handle the complete transformation cycle of four types of biomass:
- from forests: forestry waste, tree stumps, wood processing by-products, etc.
- from tree plantations: pine, coconut, palm, bamboo, etc.
- from agriculture and the agri-food industry: herbaceous plants, straw, corn stalks, nut shells, olive pits, etc.
- from wood processing: wooden packaging, black liquor from the papermaking industry, waste from landscapers, etc.
Reducing your reliance on fossil fuels
Securing your energy supplies
Cutting your energy costs
Are you a local authority or industrial customer? What are the benefits of biomass for you?
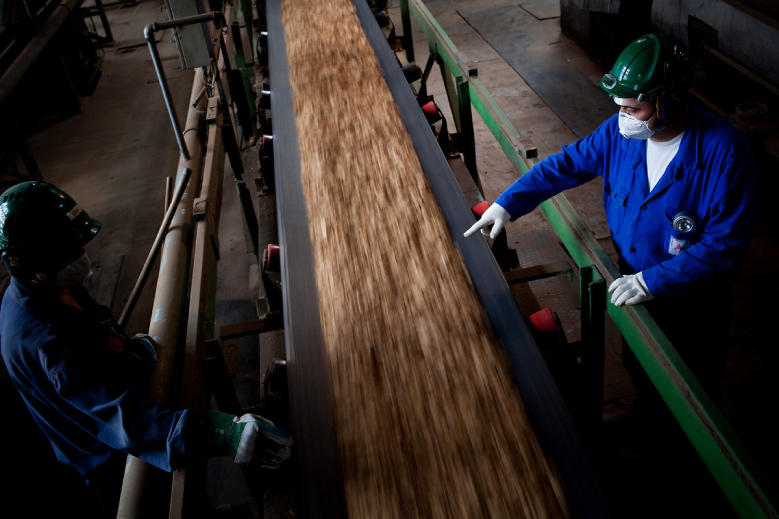
We did it!
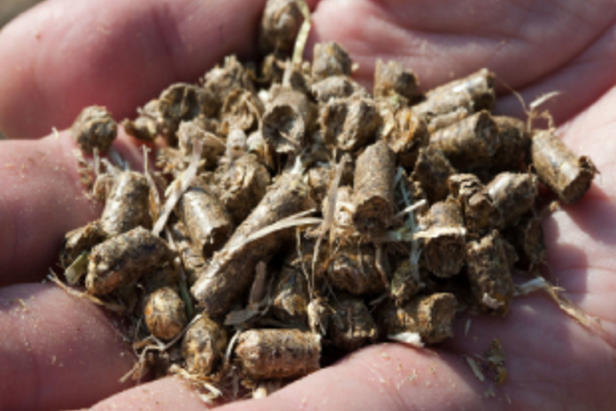
In Lódź, Poland, we recover biomass from nearby forests to optimize heat generation for the city. We have set up three cogeneration units at coal-fired power plants. These installations allow the simultaneous combustion — co-combustion — of coal and biomass sourced from regional forestry operations. This delivers a 60% cut in residents’ electricity bills.
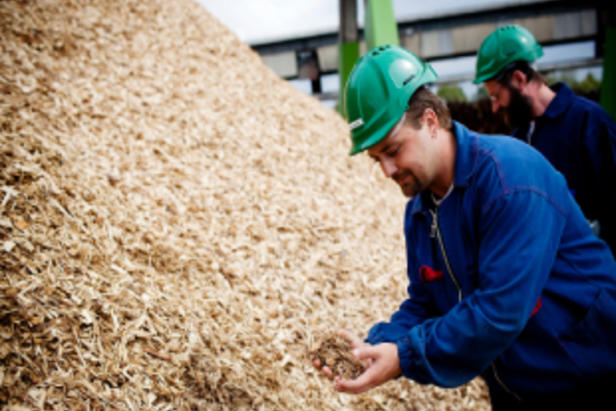
Since the end of 2013, Pécs, the fifth largest city in Hungary, has been home to Europe’s largest all-biomass cogeneration heating network. We operate two production units: a 35 MW-power plant powered by 180,000 metric tons of straw a year, and a 50 MW-power plant running on 400,000 metric tons of wood and wood residue. The recovered biomass is sourced from regional farmers and forestry operators. This means we can meet 60% of the city’s need for heating while also avoiding the annual emission of 400,000 metric tons of CO2.
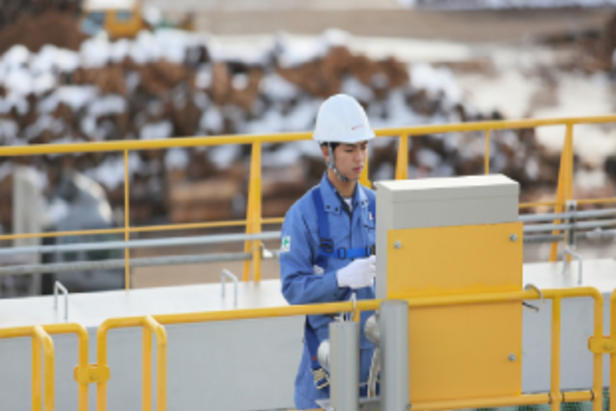
Japan
As part of a drive to develop renewable energy production in Japan, we are working with two biomass power plants, in Hitakawa and Hanamaki on Honshu Island. Every year we use wood from the local forestry industry to generate 100 GWh of electricity, enough to power 22,000 homes. This avoids emitting 40,000 metric tons of CO2 every year.